ICRYSTAL epoxy resin
Transparent epoxy resin for pouring up to 1.5 - 2 cm thick.
This UV-protected crystal resin is suitable for Resin Art and Geode Art, jewellery, key rings, bookmarks, coasters and resin decorations and is often used as a finishing layer for tables and bars due to its higher hardness and heat resistance.
Its simple 2:1 mixing ratio makes it very popular for weighing both ingredients. The low viscosity ensures better drainage of mixed bubbles. It is a high quality resin with perfect gloss and transparency of the finished products.
This resin is suitable for pouring into silicone moulds from our range up to a thickness of 1.5 - 2 cm.
The resin is supplied with hardener. The quantity purchased is the sum of the weight of components A and B.
Mixing ratio: 2A : 1B (by weight).
Producer: RESIN PRO ITALY
Clouding of the A component of resins (milky colour, white pieces, lumpiness, etc.) is a common phenomenon caused by storage at temperatures below 20 °C (in storage, during transport, etc.). If clouding is detected when casting component A, do not mix the resin with component B. First, place the sealed bottle with ingredient A in a warm water bath (50-70°C) for 20-30 minutes and the cloudiness will disappear. Let cool and then process.
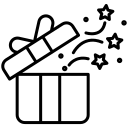
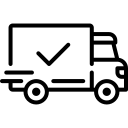
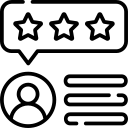
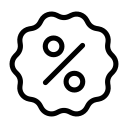
ICRYSTAL epoxy resin is a perfectly transparent crystal resin with glass-like transparency. It has an excellent UV filter and is more resistant to scratches and heat. After curing, it has a solid, mirror-shiny and completely smooth surface.
It is fully transparent and can be applied in layers of approx. 15 - 20 mm. In the case of higher castings, we recommend casting it in layers, after partial or complete hardening of the bottom layer. It can be well coloured and pigmented. It is also suitable for thin layers from 1 mm.
It cures in about 24 hours, is easy to work and polish. It has excellent mechanical properties, high strength and cohesion.
Be the first who will post an article to this item!