Liquid silicone for making molds
Silicone for the production of custom moulds that can be used not only for resin but also for other casting materials. It is very well draped and reproduces every single detail.
Its special formulation (20 Shore A) guarantees optimum results for a wide variety of applications. This makes it the ideal silicone for those who always want an excellent result in a wide variety of projects. From small reproductions of jewellery and smaller decorations to large sculptures.
The production procedure and calculation of silicone consumption can be found here.
The finished moulds are suitable for casting resin, concrete and other cold cast materials as well as wax and soap. On the other hand, they are not suitable for metals such as tin, lead, etc.
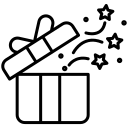
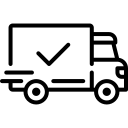
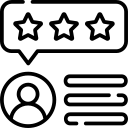
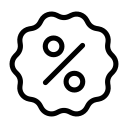
Thanks to the special texture, the moulds do not deform and at the same time ensure easy removal of the model. If the model is made of porous material or silicone, treat it first with a separator to prevent the silicone from sticking to it.
Why choose this silicone for mould making?
- Optimum hardness of cured silicone (20 Shore A) for a wide variety of applications.
- It is compatible with resins, waxes, plaster, soap or polymer paste.
- It's durable. When used correctly, the mould produced will last up to 50 perfect castings.
- It has a long workability to ensure maximum mould accuracy.
Technical features:
- Mixing ratio 100:2 by weight.
- Processing time 60-80 minutes at ambient temperature and 20 °C.
- Complete cure in 12 hours at an ambient temperature of 20 °C.
- Hardness - 20 Shore A.
- Colour white, semi-gloss.
- Viscosity: 10000 (MPa.s).
- Tensile strength >= 4,3 MPa.
- Elongation at break >= 390 %.
- Breaking strength, KN/m >= 27.
Be the first who will post an article to this item!